Honda has developed some new technology for vehicle construction, and they have applied it for the first time in the world to a mass-production vehicle; and not just any mass-production vehicle, the Honda Accord, one of the top-five selling vehicles in the United States.
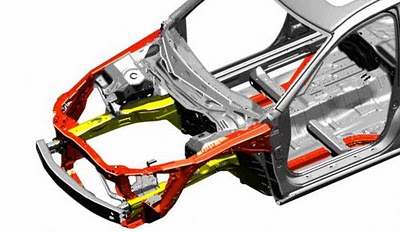
|
Cấu trúc UHSS tích hợp trên thân xe Acura TSX |
The newly redesigned 2013 Honda Accord went on sale in the United States on September 19, and its construction is the result of Honda's next-generation Advanced Compatibility Engineering (ACE) body structure which utilizes the new welding technique as well as hot-stamped and other ultra-high strength steels to build its cabin structure.
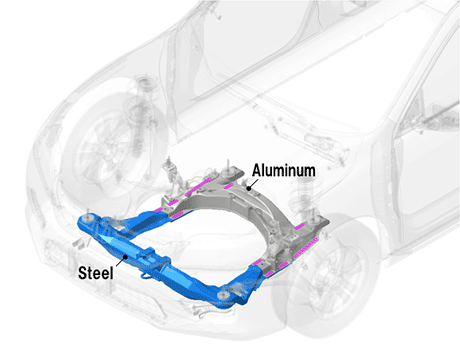
The Accord's subframe is made with a combination of steel and aluminum joined together with a process called Friction Stir Welding (FSW). The continuous weld technology generates a stable metallic bond between steel and aluminum by moving a rotating tool on the top of the aluminum which is lapped over the steel with high pressure. Honda says the resulting weld strength is equal to or greater than conventional MIG welding.
Honda also developed a non-destructive inspection system for quality control that uses a highly-sensitive infrared camera and laser beam to inspect every unit. The carmaker says the Friction Stir Welding system it developed for this process can be also be used for aluminum-to-aluminum welding and could be used for production of a full-aluminum subframe.
High Strength Steel Structure
The subframe however, should not cause many repairability issues according to I-CAR Technical Director Jason Bartanen, as Honda provides no repair procedures at all for the part, and specifies complete replacement only.
"What will cause some issues is the high strength steel used in this car's body structure," said Bartanen speaking from the I-CAR Tech Centre in Appleton, Wisconsin.
The newly redesigned 2013 Accord body uses 55.8-percent high-tensile steel, more than in any previous Accord. And 17.2-percent of the steel is grade 780, 980 and 1,500 MPa, extremely high grades that have never before been used in any Accord, and in fact, very few other cars, according to Bartanen.
"This is one of the first cars to use such high strength steel (1500 MPa) in its body structure," says Bartanen. "Most applications only use it only for bumper beams. But the new Accord uses ultra-high strength steel in its A pillar and B pillar reinforcements as well as its rocker reinforcements. Honda is requiring MIG brazing only in these areas.
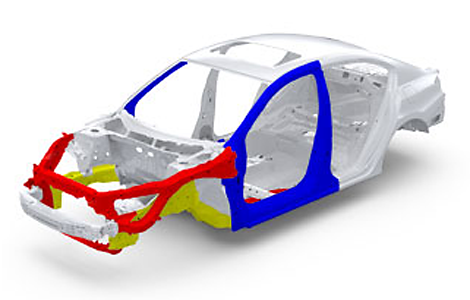
While Honda is not the very first to build such a body structure, none of the previous vehicles even come close to the sales volume of the Accord. "The Volvo XC60 is also using similar ultra-high strength steel (1,500 MPa) in the structure," Bartanen noted.
The Accord has historically sold between 250,000 and 400,000 units a year compared to XC60 sales of approximately 25,000.
Bartanen said I-CAR is currently updating its Honda and Acura training available online. The new Accord will be covered in I-CAR's Collision Repair Overview for Honda and Acura Vehicles (HON01) and should be available within the next few months.
"We have an Accord body in white on its way here right now," Bartanen noted. "We are going to paint it to show the various steels used in this car and prepare it for display at the SEMA show."
The ninth generation Accord, which also contains Forward Collision Warning and Lane Departure Warning technologies, officially debuted at dealerships across the U.S. on September 19 at a base price of $21,680 plus destination charge.